In the competitive realm of battery manufacturing, ensuring quality at every stage of production is crucial. EVE Energy stands out through its rigorous on-site quality management system for Lithium Iron Phosphate (LFP) prismatic cells. This blog post delves into the sophisticated processes and measures EVE employs to maintain superior product quality and safety, focusing on their LFP prismatic cells.
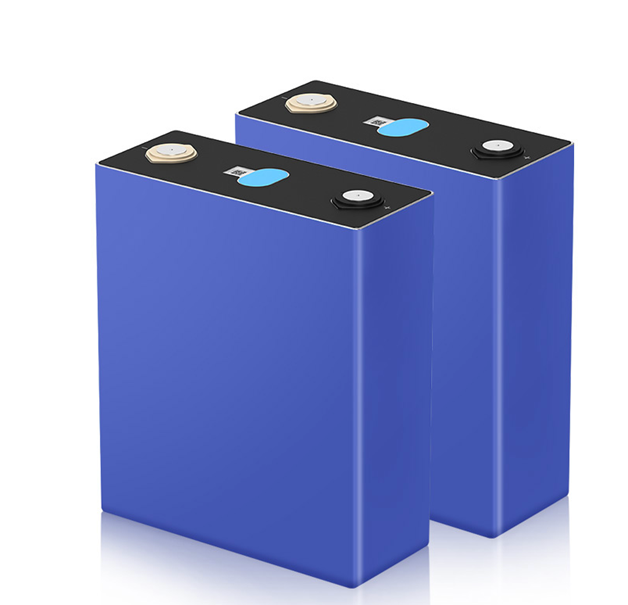
Comprehensive On-Site Quality Management
EVE’s approach to quality management is holistic, emphasizing the meticulous control of all elements involved in the manufacturing process:
The Seven Elements of Quality
EVE’s strategy revolves around seven key factors:
– Manpower: Ensuring all staff are well-trained and adhere to strict operational standards.
– Machine: Utilizing state-of-the-art machinery that is regularly maintained and updated.
– Material: Sourcing high-quality materials that meet rigorous standards.
– Method: Implementing standardized procedures to ensure consistency and efficiency.
– Environment: Maintaining a controlled environment to prevent any contamination or variability in production.
– Testing: Conducting comprehensive tests at various stages of production to validate quality.
– Management: Overseeing all aspects of the manufacturing process to ensure compliance with quality standards.
No Unauthorized Motion
Under the principle of “no unauthorized motion,” EVE enforces strict protocols to minimize any unnecessary actions that could compromise quality. This is part of their broader lean management strategy, which is supported by the QMS (Quality Management System) that provides real-time quality data and analytics.
Lean Management and Continuous Improvement
Adopting lean management principles, EVE streamlines every aspect of production to enhance efficiency and reduce waste, relying on the robust QMS to guide decision-making and improvements.
Rigorous Auditing and Monitoring
To ensure the fidelity of on-site management, EVE conducts:
– Special Audits: Targeted audits focusing on specific areas of concern.
– On-Site Audits: Regular and thorough reviews of the manufacturing processes.
– Cross-Audits: Audits conducted by different teams to ensure unbiased evaluations.
These audits help maintain strict adherence to quality standards and identify areas for improvement.
PDCA Cycle and QCC Activities
EVE leverages the PDCA (Plan-Do-Check-Act) cycle to drive continuous improvement. Quality Control Circle (QCC) activities are integral to this process, involving teams in problem-solving exercises to enhance product quality.
Impact on Product Quality and Safety
The meticulous attention to quality management has yielded significant improvements in the cleanliness of workshops and the overall manufacturing process. Notably, EVE has achieved a more than 50% improvement in the K value (a measure of the voltage drop of lithium-ion batteries per unit time). This enhancement not only boosts the performance of the batteries but also their safety, ensuring that EVE’s LFP prismatic cells meet the highest standards.
Conclusion: A Benchmark in Battery Manufacturing
EVE’s on-site quality management system sets a benchmark in the battery manufacturing industry, particularly for LFP prismatic cells. Through stringent controls, continuous monitoring, and relentless improvement, EVE ensures that each cell produced not only meets but often exceeds the expected standards of quality and safety. Such dedication to quality not only enhances the reliability of EVE’s products but also reinforces the trust placed in them by industries worldwide. For anyone seeking dependable, high-quality battery solutions, EVE’s LFP prismatic cells represent a premier choice, backed by a commitment to excellence that is evident in every aspect of their production.